WHAT IS THE DUOLINE PROCESS?
DUOLINE is an internal lining system produced by inserting a rigid plastic tube inside steel tubing and filling the annular space with a mortar. Ends of the liner are flared to give a square shoulder. This provides a landing area for the corrosion barrier ring in the coupling. DUOLINE stops corrosion where other systems fail! Result: Bottom line savings through fewer well interventions.
When corrosion starts in downhole tubing, the string soon fails. The result is downtime and increased operation costs for workovers and tubing pulls. DUOLINE stops corrosion where alternate lining or coating systems soon fail.
Applications:
- CO2 Injection Wells (WAG)
- Oil and Gas Producing Wells
- Waterflood Injection Wells
- Brinewater/Chemical Disposal Wells
- Transportation Pipelines
- Sour Gas Service
- Geo Thermal wells
- Carbon Capture & Storage (CCS)
Benefits of Duoline:
- Over 100 million feet installed
- 40 year history of leadership
- Wireline abrasion resistant
- API & Premium downhole connections
- Welded & threaded pipelines
- This unique lining process has proven to be the most successful system for the prevention of downhole tubular.
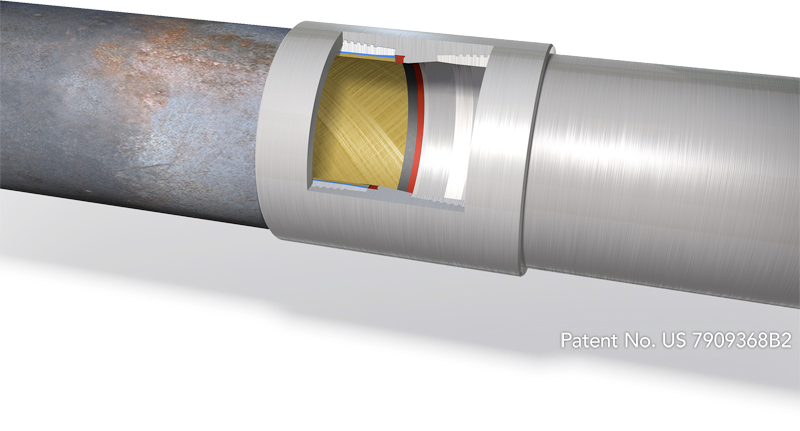
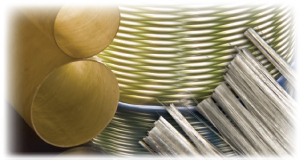
Whether the applications call for new steel tubing with premium gas tight connections, or reclamation of used tubing with API type threads, DUOLINE can be applied to satisfy a wide range of applications and customer needs. DUOLINE has a reputation as “The Lining of Choice” in CO2 injection and waterflood injection fields. Deep gas production and gas-lifted oil production wells have also been a target application for use of the DUOLINE lining system.
Duoline Technologies offers a variety of liner selections that match material performance in your specific application. DUOLINE 10, DUOLINE 20 and ADVANCED DUOLINE LINER SYSTEMS offer solutions to nearly all downhole environments from shallow brine water disposal wells to deep-hot-gas production in both onshore and offshore wells.
The unique process of inserting a rigid plastic or GRE composite (Glass Reinforced Epoxy) liner sleeve inside the pipe eliminates the “holiday” potential created by IPC coating processes. A grouting layer of cement material is placed in the annular space under pressure using a tightly controlled process. The DUOLINE process does not depend on bonding or adherence of the liner to the steel pipe wall. This benefit, combined with the high hoop strength of the GRE liners, (DUOLINE 20 & DUOLINE 30) provides the most resilient lining system for high-pressure gas service or water systems with high CO2 or H2S content.
A most important consideration for any corrosion resistant piping system is protection of the connection area, which is the strength of the DUOLINE process. After all, what benefit is realized from a premium pipe coating or lining that permits connection corrosion? Most coated tubing corrosion failures originate in the connection area. Duoline Technologies employs a reinforced elastomeric corrosion barrier ring (CBR), which is compressed between the liners in the connection make-up process. This compressed CBR is held in place by the liner, and prevents passing fluids from causing the all-too-common coupling failure. Duoline Technologies manufactures a metal wire reinforced nitrile elastomer ring for API connections. A fiber-glass reinforced PTFE ring is available for premium gas tight connections.
Duoline Technologies recommends the presence of a trained DUOLINE technician when DUOLINE is installed or repaired at the well site. In addition, a number of service companies throughout the world have technicians who have been trained by Duoline Technologies or MaxTube to run or repair DUOLINE.