EROSIONAL VELOCITY THROUGH DUOLINE 20™ GRE LINED TUBING
Erosion Damage in Steel Tubulars
In order to avoid erosion damage in steel pipe, the common practice is to calculate the guiding velocity Ve within which the erosion is not expected to occur. This is done using the API RP 14 E equation (API, 1981, 1991)
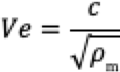
where C is the empirical constant and ρm is the gas-liquid mixture density at flowing conditions lb/ft3. The velocity limit provided by the equation is used to control the removal of the inhibitor film or the corrosion by product. Duoline 20 does not depend on inhibition films.
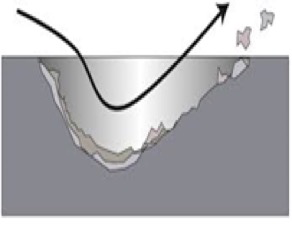
What is Duoline 20 GRE Lined Tubing?
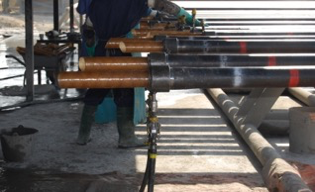
Solid GRE tube is inserted into carbon steel tubing
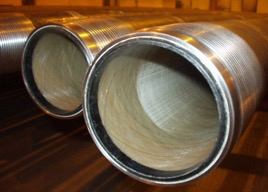
Ends are protected with over arching flares
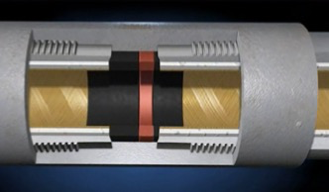
Fully protected connection area with a seal ring between the flares
Since Duoline 20 does not depend on inhibition films, concepts such as shear stress are considered more representative of the erosion. Shear stress is the force applied by flowing fluids to its boundary. Shear stress is a better predictor of erosion potential than velocity, because it considers the actual force of the flow on the surface of the pipe. Shear stress can be calculated using in the NORSOK M506 R2 tool, available on the internet.
Duoline has been tested upto 307 Pa which resulted when:
- 13,500 bwpd flowed through 3 ½” Duoline GRE lined tubing (ID 2.75”)
- 152 mmscfd of gas flowed through 7 5/8” Duoline GRE lined tubing (ID 6.45”)
It is recommended that the relevant process data is plugged into the NORSOK M506 R2 tool to calculate the shear stress and confirm that it is within the 307 Pa test result.
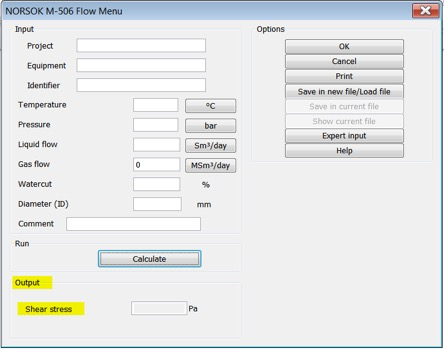
Erosion Tests by Operators
BP SPE paper 115313, “Alternatives To 25% Chrome For Water-Injection Tubing In Deep Water” explains testing on Duoline GRE for application in deep water high rate injection wells. Erosion modeling using highly concentrated erodent (2% w/w) under typical injection flow (at 5 m/s) showed no measurable wear while a simulating 18 months of service. A full-scale flow-loop test was also performed to confirm this performance.
ENI paper “Fiberglass Liner in Production and Water Injection Wells: Eni Experiences and Feedback” explains their direct impact and flow loop testing on Duoline GRE.
24 Direct Impact Tests were performed using solid concentrations from 0.70% to 1.30%, at varying nozzle-to-specimen angles, using jet velocities from 21 – 35 m/s, for up to 30 minutes. Erosion Rates from comparative tests on Inconel material were found to be very close to the values obtained by Duoline GRE. The paper confirms that Duoline shows a high resistance to erosion at high velocities and solids loadings.
During Flow Loop Erosion Testing, the Duoline GRE Lined pipe was exposed to a mix of water and sand flowing at 8.4 m/s. Grain denisity was 2500 kg/cu.m and grain sizes d10=170 μm, d50=250 μm, and d90=350 μm. Visual inspection of the internal surface of the Duoline GRE lining did not reveal any sign of erosion. The thickness of the Duoline GRE lining remained unchanged confirming the absence of measurable / detectable mass removal.
Operator Documented Field Experiences
Duoline lined tubing is flowing 110 mmscfd gas for over 10 years through 7” Duoline lined tubing. Operator findings from these wells are published as follows:
- Shell Case Study (SPE Approved Abstract) on Successful Hydraulic Fracture Operation through GRE Composite Fibreglass Lined Carbon Steel String 90,000 lbs of proppants injected at 4,000 psi for 30 minutes (28,800 bpd flowrate). After 24 hours of flow back there has been no reported damage to Duoline GRE.
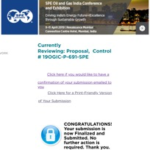
- 2013 Petronas IPTC 16472 Pilot Application of GRE Lined Tubing for Big Bore Gas Producer wells
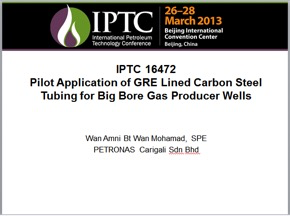
- 2017 Petronas SPE Paper SPE-188982-MS Gas Field Subsurface Integrity: Performance Analysis of GRE Lined Tubing at High H2S Wells at Offshore Caspian Sea
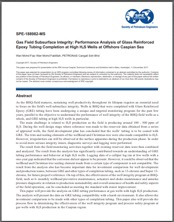